This week was all about metal research and testing.
Understanding Galvanized Metal
This material is formed by coating steel with zinc, providing excellent rust resistance. The result is a robust, durable product with a rugged look that many consumers love.
The appeal of galvanized metal extends beyond aesthetics. Research shows that coolers featuring this material can last up to 15 years, significantly longer than conventional plastic options. This durability means fewer replacements and a better return on investment.


The above pictures is a cooler designed to keep delivered milk cold as it sits on home owners door steps. The Wengert's Dairy delivered in this way during the 1930's.
Working on build techniques to deliver the right insert.
The work of a DIY'er is never complete! After hours of research and playing around with the below tools and test metal sheet samples, here is what I have come to.
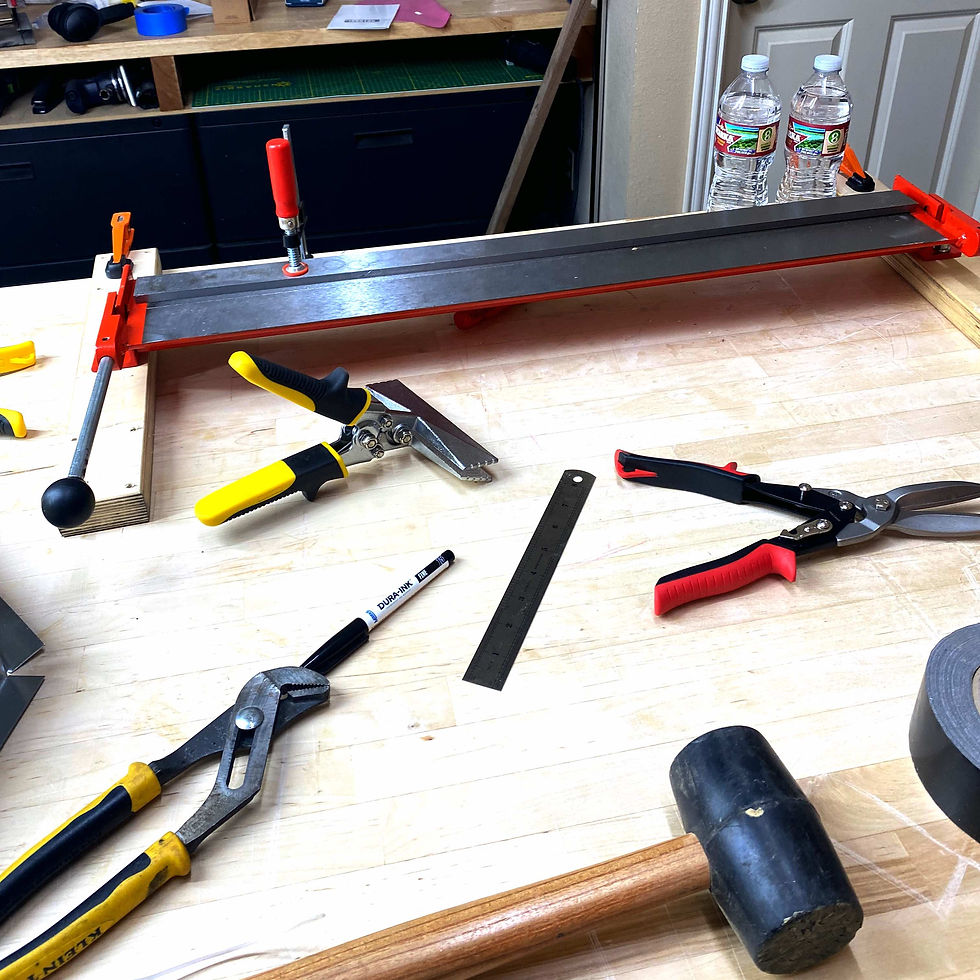
I worked with a strip of 22 gauge of galvanized sheet metal and bent it into an octagon (ish) shape.

Then I created what's called a coffin lock. It's a process of bending the seam so it has a slot that both sides can fit together. the gap on the top and bottom are here because I need to bend to top and bottom of the cooler walls.

Like this.

My earlier testing made me realize that the coffin lock needs to be on the outside so as to show a clean inside seam.

Like this one.

Then it's off to figuring out how to attach the base. Here is what I have so far. Place a bottom sheet under the octagon walls and bend the edges over the 90 degree base bend.

So now what do I do to make it water proof? I can't have it welded. While the sheet metal is extremely strong and rigid, it's not thick enough to weld the traditional method, plus it will loose the galvanized properties near the welded seam. So I started investigating soldering. And again after a lot of research, I found a method that works great.
here are a few youtube videos that put me in this direction.
Below are test seams that I soldered. Not pretty but it confirmed my path and gave me enough insight into the process to take this path.

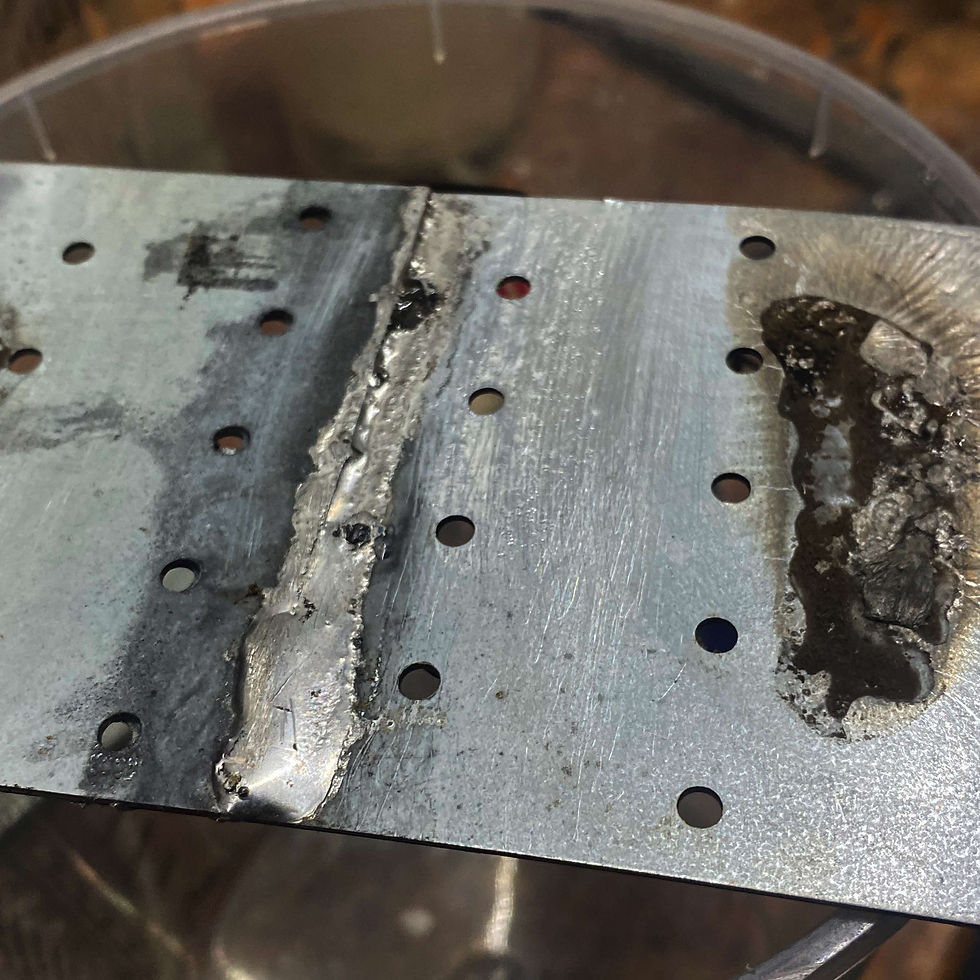
And then I said to myself, "not everything has to be DIY! This is already a complicated build, why not look for an expert in my area to see if they can help?
And that's when I found Alex Contreras a metal fabricator at Almighty Garage in Waxahachie Texas! We had a nice chat where I explained what I am doing and he offered to make the liner for me! I still have to do the soldering and attach the bottom drain, but Alex is a professional with deep experience with the commercial grade tools to make this octagon liner the right way. His coffin lock will be much tighter than I could do! He will also be able to spot weld the base and wall seam.
I plan on meeting him there next weekend to see his magic. I will take pics of his process, tools and great work.

Mark Petrilla
It’s impressive to see the level of detail and effort you put into this build! Can’t wait to see the final product and learn more about Alex’s fabrication process. Thank you for sharing the process! It’s been so neat to follow along!